At Amazon, we’re always working to improve and harness new technologies to better support our workforce, customers and the communities we operate in. Since 2011, we’ve invested more than A$15 billion across all of our businesses in Australia, including more than A$5 billion in 2022 alone.
Earlier this week, Caroline Kennedy, U.S. Ambassador to Australia, visited BWU2 in western Sydney, our first robotics fulfilment centre in the southern hemisphere, where we introduced her to some of our newest innovations and initiatives in Australia, and, most importantly, our people.
Follow Ambassador Kennedy on her journey as she discovers some of our most exciting technologies, and get an exclusive behind-the-scenes look at what goes on in the state-of-the-art facility.
Stop 1: Arrival at BWU2
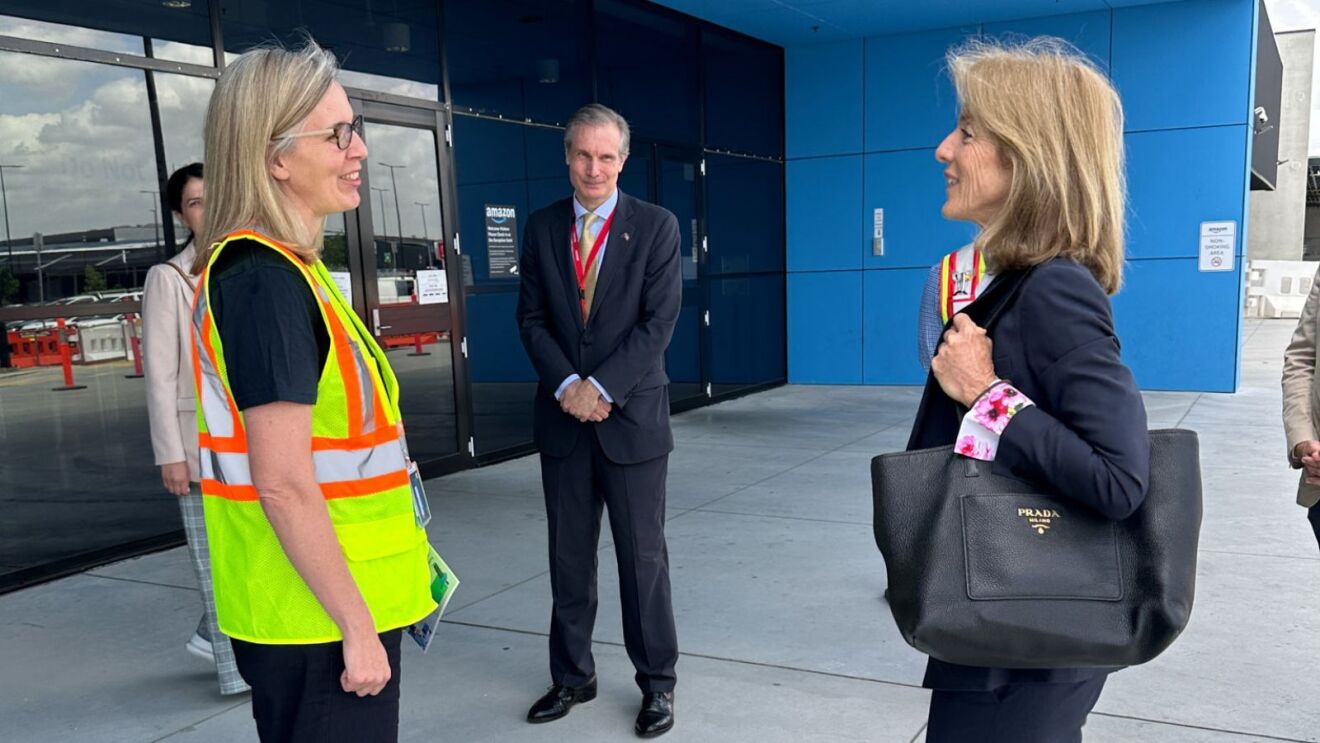
This important site—one of six fulfilment centres and 12 logistics sites across the country—is the largest warehouse ever built in Australia. At 200,000 sqm the site is the size of Taronga Zoo, or 24 rugby league fields! It houses up 20 million items and has the capacity to process hundreds of thousands of orders a day. It has also created more than 1,500 jobs. Crucially, it’s strategically located within a 12-hour drive to 80% of Australia’s population, which enables faster deliveries to our customers.
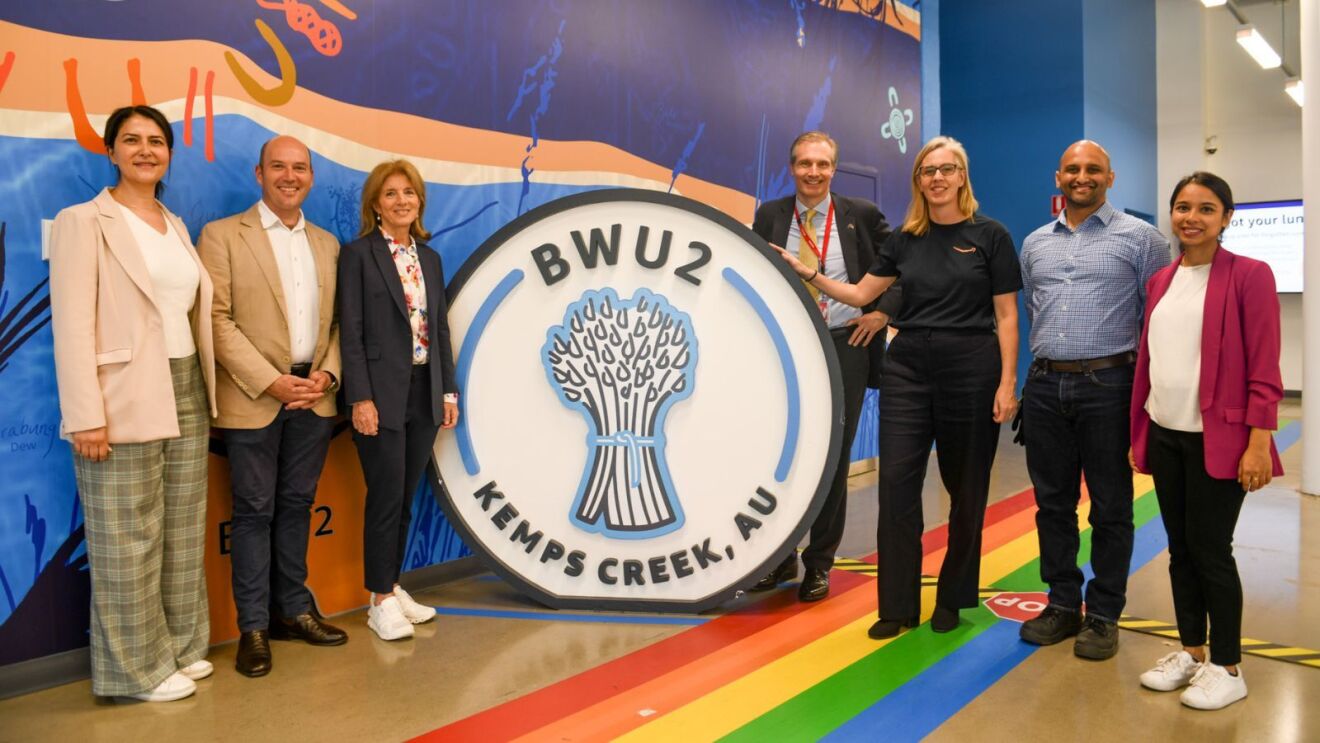
In the foyer is a meaningful artwork that was created specially for the site by three Sydney artists. Titled Ngarra Naangun Buru Bamurawa (‘Coming together we see buru on the place of grasses’), the artwork conveys connection to Country and Language while merging traditional Dharug and contemporary cultures.
Stop 2: The robotics floor
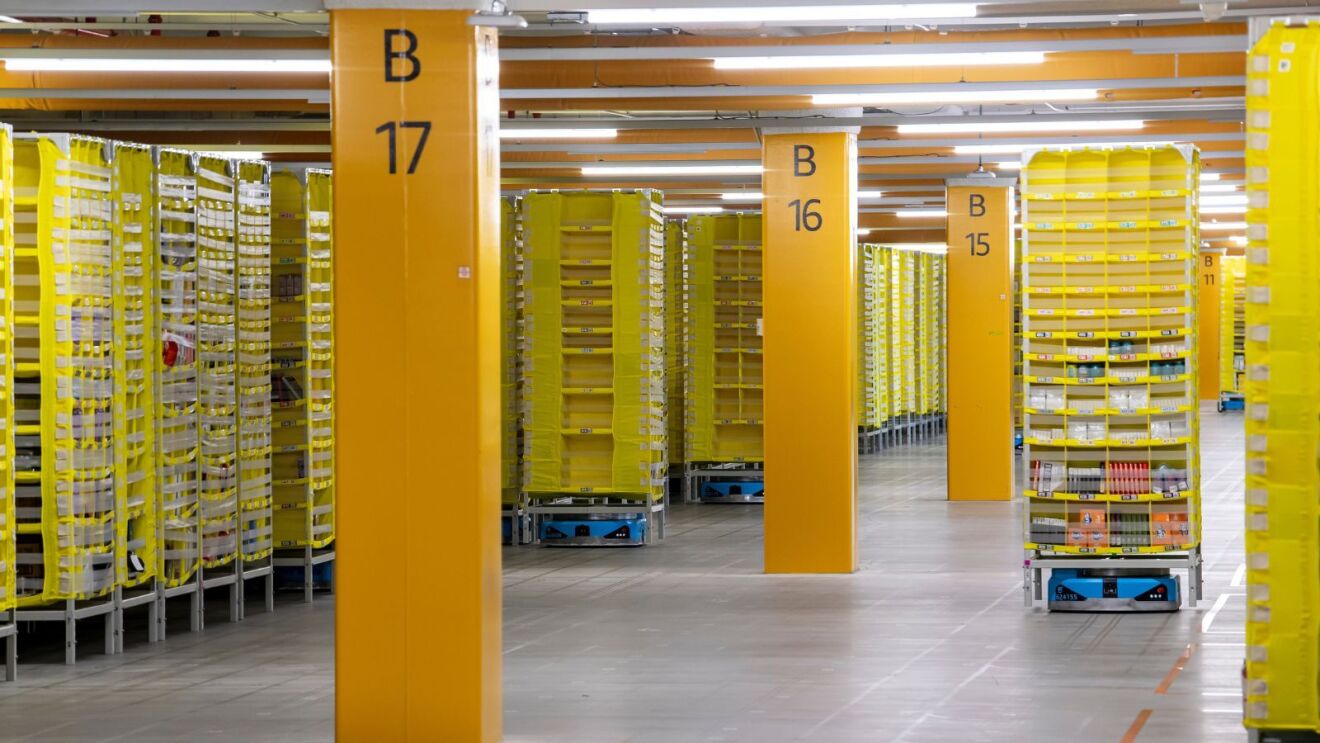
This is one of three robotics floors where products are held after they’re received from some of the thousands of independent sellers who use Amazon’s fulfilment network and before they’re packed for delivery. Each floor is identical, with the inventory pods in the middle, and the stow and pick stations around them.
Robotics drive units help to move the products around—each one weighs more than 130 kilograms and can lift up to 680 kilograms of inventory. There are more than 100,000 QR codes on the floor that help scanners at the bottom of the units navigate which direction to travel in.
The robotic field is surrounded by 2.5km of special fencing, and no one can enter without a robotic vest for safety reasons. The robots automatically stop if they sense a person or any object inside the field.
Stop 3: Meet an Amnesty Floor Responder
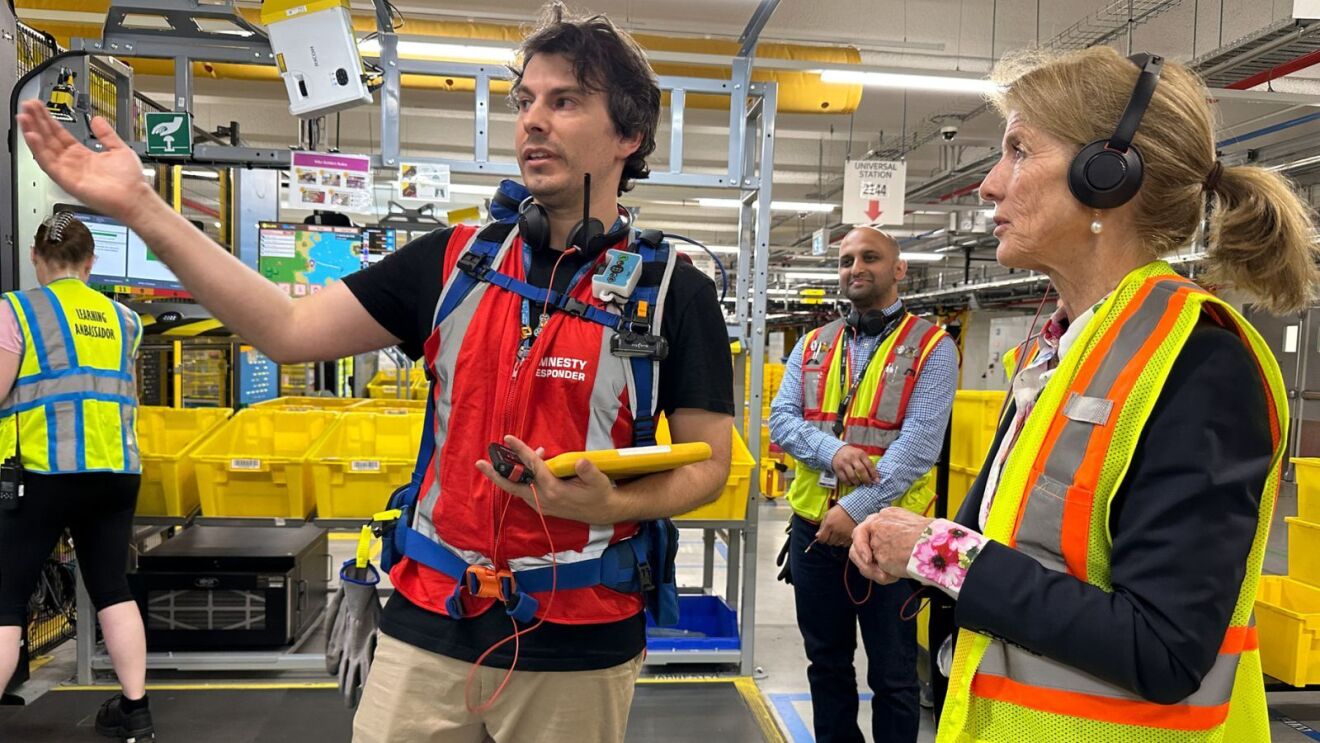
Our Amnesty Floor Responders are technicians who help make sure operations on our robotics floors run smoothly. For example, if a product falls out of its pod, an Amnesty Responder will enter the field to remove the item wearing a special robotic safety vest that uses AI, sensors, and enhanced communications to send signals to the robotics drive units. This tells the robots where the technician is and ensures that they automatically slow down, come to a complete stop or update their route to avoid that location.
Stop 4: Stowing process
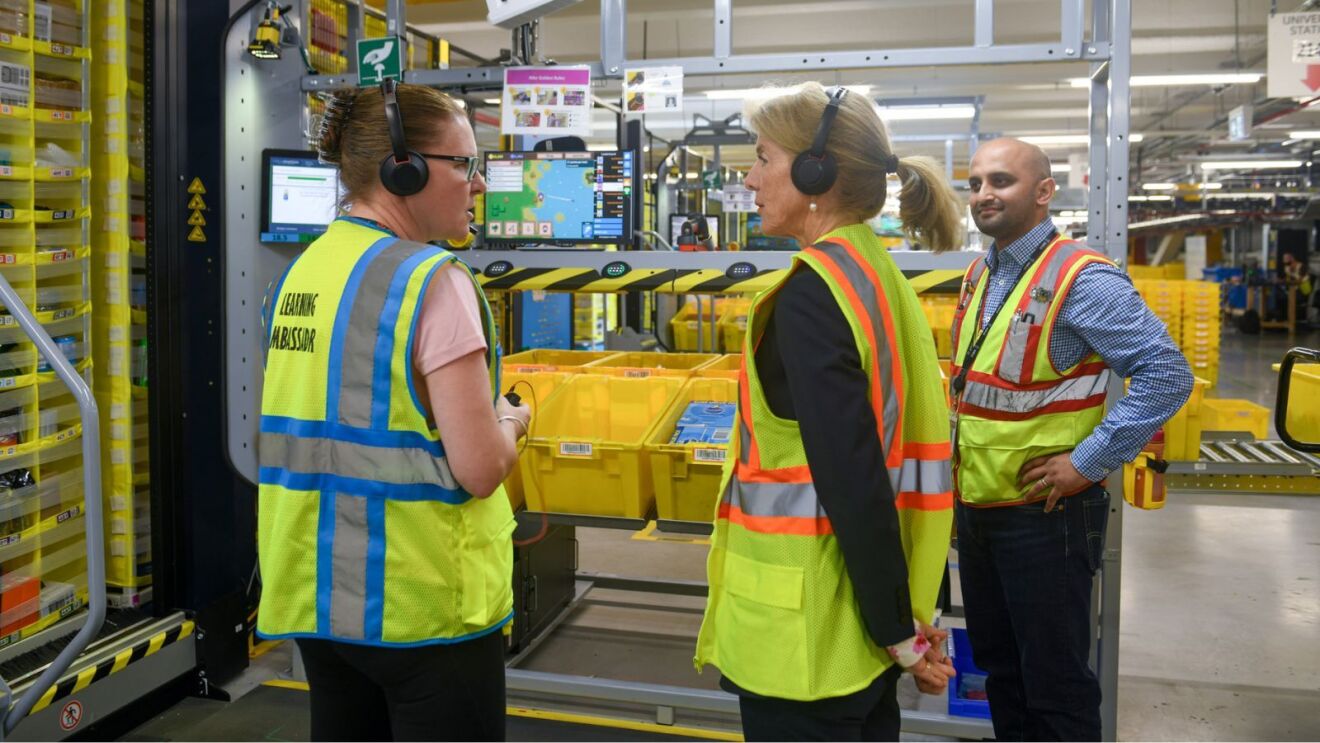
Robots work collaboratively with our team members by moving pods of inventory to them, reducing the time and effort that would otherwise be required to stow products for sale or pick them for new customer orders.
One of the main benefits of incorporating robotics into the process is that it improves selection for customers. At a robotics site, because we don’t need space for people to walk among the shelving, we can fit 40% more inventory than in a traditional manual set up. That means we have capacity to fit a lot more items and support many more sellers. Did you know: There are already more than 14,000 Australian sellers in Amazon’s stores globally, many of which are small and medium businesses?
Stop 5: Packing process
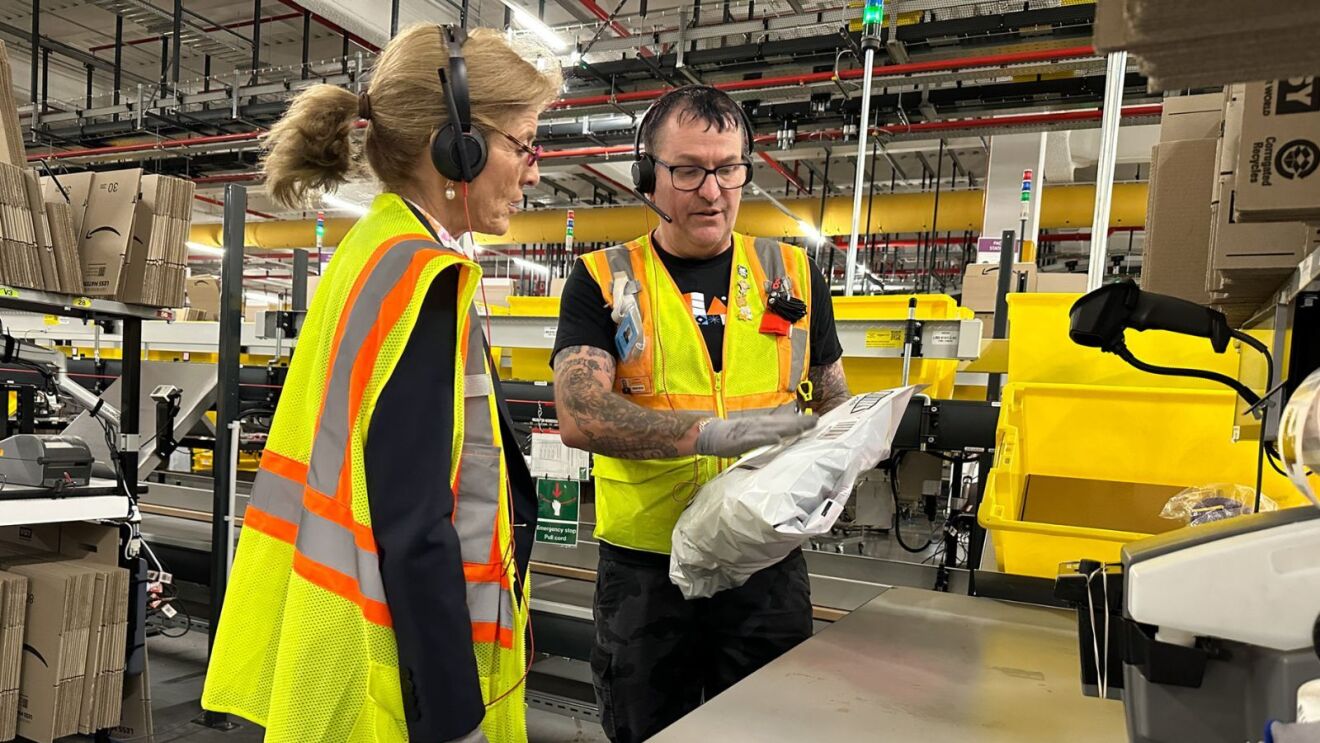
At our packing stations, computers automatically tell packers what size box to use for a particular order, and dispense the exact length of tape needed, which reduces the amount of packaging used. A special barcode is also applied that tells us everything we need to know about the order—like a license plate for a car—while still keeping the customer’s details confidential.
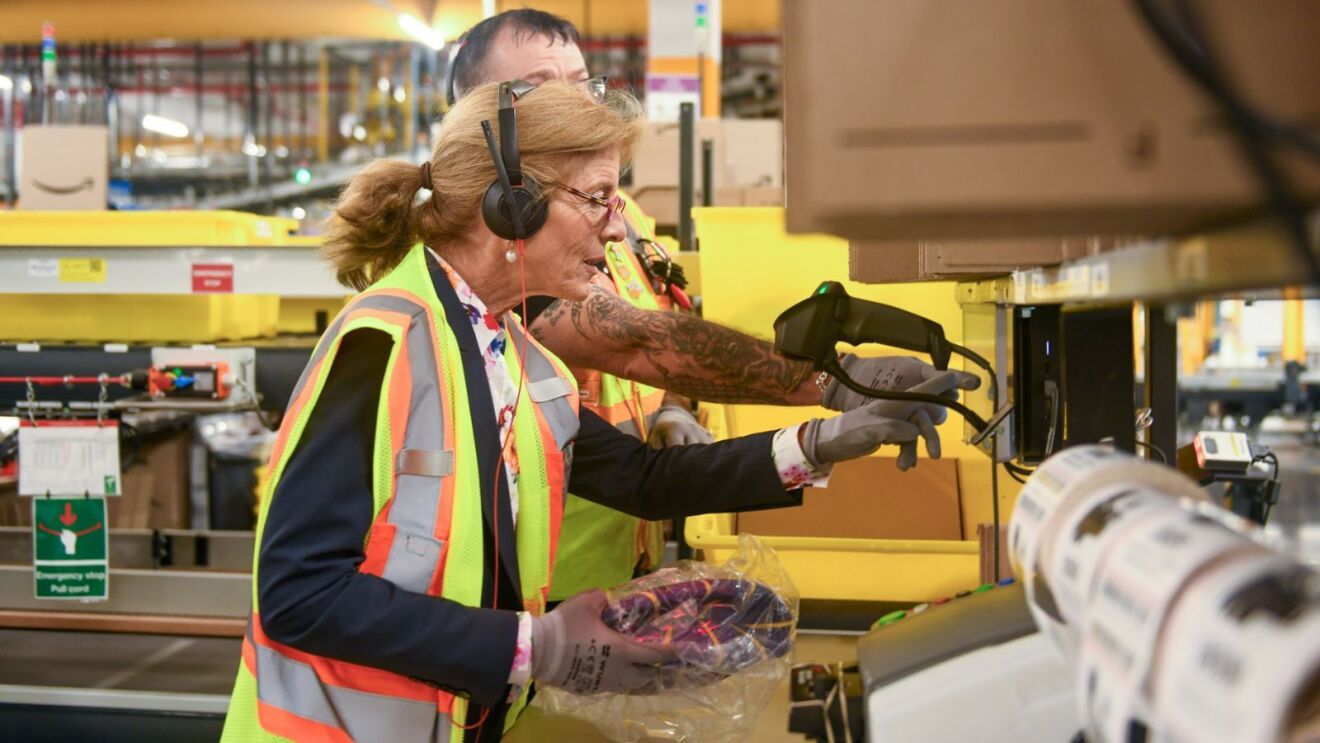
Then it goes to a machine that scans this barcode, weighs and measures the box, and applies a shipping label with a robotic arm, all within seconds. This is the first time the customer’s name and address are added to the package. In the majority of cases, packages will arrive within two business days of the order being placed, and for many people within one day.
Some orders don’t even need an additional Amazon box or bag. Thanks to our Ships in Product Packaging programme, products that are capable of being shipped safely may be sent to customers in the manufacturer’s original packaging. It’s one of the ways we’re working to reduce packaging.
Stop 6: Disaster Relief Hub
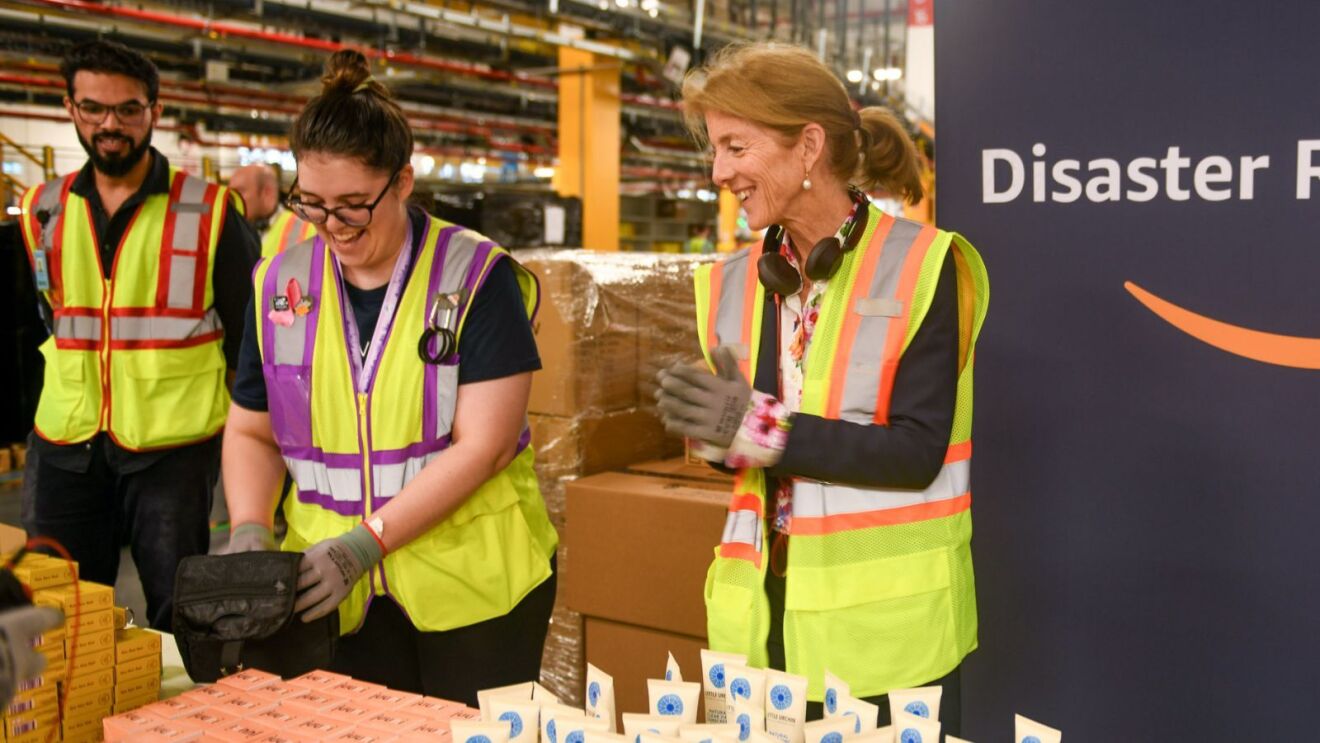
Apart from serving as a fulfilment centre, BWU2 is home to the second-largest of our six Disaster Relief Hubs across Australia. Here, more than 70,000 relief items are stored and ready to be distributed in the event of a natural disaster.
Amazon uses data analysis and insights from its non-profit partners to identify the relief items most commonly needed on the ground when a disaster strikes. Since 2019, we have sourced and dispatched more than 545,000 relief items and supported our non-profit partners through 13 disasters in Australia including bushfires, floods and COVID outbreaks.
We hope you enjoyed this tour of our Sydney robotics site with Ambassador Kennedy! Next, explore our corporate office in Sydney here.